Avolites celebrated its 45th anniversary in 2021. Always a world leader in the innovation of visual control systems, the company, the technology, and the creative scope of the artists that use it have all changed massively in the years since.
From modest beginnings established in 1976 under a railway arch in Hammersmith, London, through to its first touring dimmer rack, the landmark Avolites FD dimmer, to the launch of its latest flagship Diamond 9 console early in 2021, the company has been at the forefront of technological change in the lighting events industry.
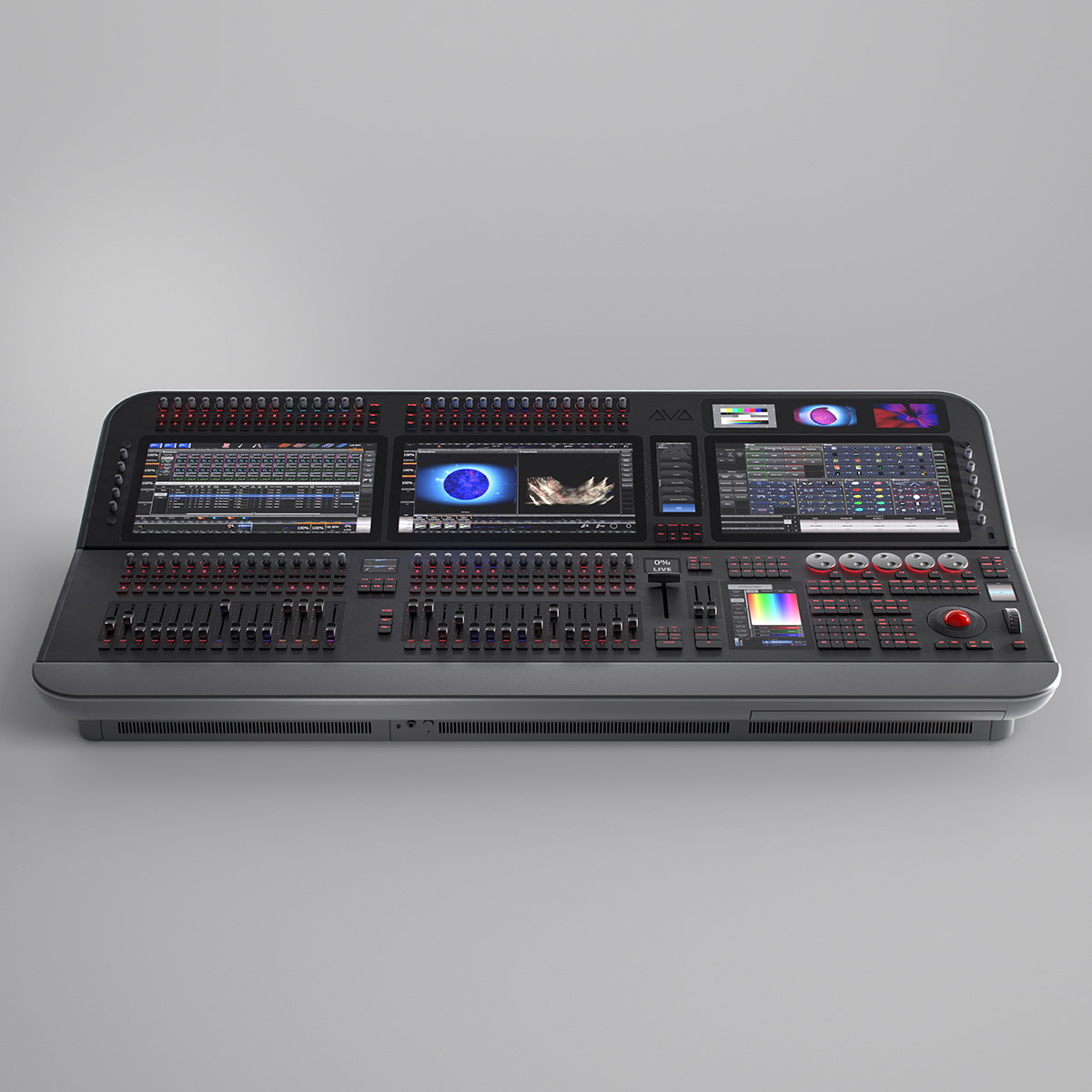
Avolites has always believed in the power of technology innovation to improve creative expression, and has coupled that approach with bullet-proof reliability, ergonomically designed interfaces allowing for ever-more artistic freedom, top-grade components, quality finish, and inspired design. As such it has played a key role in enabling shows to become bigger, more demanding, and ever-more immersive over the decades, ensuring that the multimedia visual canvases that delight audiences worldwide fulfil the increasingly demanding ambitions of their designers.
This is both its story and the story of the changes that have taken the industry from switching single spots and coloured gels to the massive multimedia extravaganzas that centre such events as the London 2012 Opening Ceremony, the largest touring shows, the biggest stage productions, and the world’s leading nightclubs.
1976 and all that
Avolites was set up by Ian Walley, who had obtained a Bachelor of Science in Mechanical Engineering and went on to find work in the music business providing stage lighting touring services for rock bands.
During the years 1974 and 1975, Walley was employed by Scope International Equipment Hire to construct and operate on the road its three Genie stage lighting rigs, effectively making him a stage lighting electrician, rigger and lighting designer. In other words, an all-round roadie. During this time, he toured with various bands and operated as Lighting Designer for Barclay James Harvest, Caravan, and other acts. Thanks to his habit of turning up at venues and carefully monitoring the electricity supply available with his trusty Model 8 AVOMETER (AVO in this case standing for Amps, Volts, and Ohms) he soon earned the nickname AVO himself.
In these early days working on the road touring with bands and setting up their equipment, Walley soon became frustrated with the almost daily routine of having to repair the lighting control equipment used at that time. He was quite sure that he could design and manufacture a far more reliable, fast-rig system. In discussions with Barclay James Harvest’s management and Lindsay Brown in particular he secured an assurance that if he designed and built his own lighting rig, the band would not only continue to employ him as their Lighting Designer but also use the company he had recently set up for its lighting equipment hire.
Thus Avolites, which Walley set up in his own warehouse in a Stamford Brook railway arch in Ravenscourt Park, Hammersmith, London in February 1976, got its first big break.
Avolites’ first carefully designed and constructed rig comprised a 40-foot and 30-foot truss controlled by Walley’s self-designed and self-constructed Matrix Lighting Desk and 19-inch Modular Dimming Rack. Two friends, brothers Paul and Dick Ollett who worked on the road with ESP Lighting and TFA Electrosound, assisted him with his initial equipment and control designs. This included the creation of the industry’s first multi-pinned ‘Twofer Box’ to enable patching and series connections of the 110 volt PAR 64 lamps to the 240v UK and European mains supplies.
Once the new equipment hit the road, word quickly spread of its excellence, its reliability, controllability, and fast set-up. Worldwide demand for Avolites’ lighting control systems rapidly followed.
In March 1977, Avolites Production Company Limited was born with Walley, the founder, owner and Managing Director. A change of emphasis saw the company gradually pivot from lighting touring production to lighting control system manufacturing; new premises were secured in Shepherd’s Bush and then in a very smart move considering the London property market, the firm acquired its current Park Royal HQ in 1985. As it expanded Walley asked three fellow roadies, Paul Ollett, Murray Thomas and Clive Standley, to join the company full time as fellow board members and directors.
The AVO meter
The AVOMETER (AVO for Amps, Volts, and Ohms) started life in 1923 and was possibly the most ubiquitous piece of electronics testing equipment ever invented. Alongside the iconic design (though you really have to hold the unit upside down to appreciate the full impact of the two switches and the ‘smiley’ meter scale), AVO multimeters were renowned for their reliability and robustness, and boasted features that endeared them to generations of electrical and electronic engineers.
By 1965, the company had already created over one million AVOMETERS. Though production of the iconic Model 8 finally ceased in 2008 when the last Mk VII meter rolled off the production line, the company, now called Megger, still manufactures the AVO800 series of digital multimeters. There are meanwhile plenty of the original units in varying conditions available on eBay.
Diamonds, Sapphires, and Pearls
Over the decades, Avolites has manufactured a wide range of lighting control products, media servers, accessories, and software, but it is fair to say that it is probably best known for its range of lighting control consoles and dimmer racks.
These include: the first generation of consoles designed to control the new intelligent lighting products that were emerging onto the market in the 1990s, such as the Sapphire, Pearl, and first Diamond consoles; the Art dimmer/distribution series followed by the PowerCube dimmer/distribution units in the 2000s; and the launch of its own game-changing Titan lighting control software in 2009.
Back then, as it is now, at the heart of every technology decision or innovation lay the requirements of the company’s customers: the lighting and video designers and operators who were going to use the tools that it made. Listening to what they wanted made sound business sense, and what they wanted was Diamonds.
The Diamond heritage goes back to the early 1980’s and those early days under the Stamford Brook railway arches of the District Tube Line with the arrival of the 8100 console series. These were custom built units specifically designed for the demands of touring. Using blue anodised panels and engraved lettering filled in white (to enable easy reading in dark conditions), the consoles had cast aluminum trim and even featured leather armrests for comfort to reduce operator fatigue. For accurate cueing they used C&K switches, which somewhat remarkably is the same switch that is used in its distant descendant, the D9, today and all the current consoles (more of that later).
The 80-100 was a classic design and one that pretty much set the style for touring lighting consoles for generations to come. But the next unit out of the company’s R&D efforts was set to be the biggest game changer in Avolites’ long history, the QM series.
The QM series is a part of rock history in particular. Launched in 1983, it added microprocessor technology for storing cues and sequences to the fast Swap and Add model of operation from the analogue 8100 series. The onboard computerisation enabled users to record scenes for multiple playbacks, and featured a highly readable and programmable electronic legend — hence the name QM (Cue Master).
To put its introduction of microprocessors and taking lighting control into the digital age in context, Apple introduced the Lisa computer that year which was the first commercial computer with a graphical user interface, and the Apple IIe also shipped with a massive 64kb RAM.
The QM series was genuinely pioneering, and made its name for itself on Queen’s 1984/85 The Works Tour under Lighting Director Jimmy Barnett. Indeed, so popular did the console become, that in the middle of the decade 17 out of the 20 biggest grossing tours were driven by an Avolites QM500 console, and there are more than one floating about to this day that claim to be Barnett’s original machine used on the tour.
There were other significant milestones too away from the increasingly large rock arenas that became the QM 500’s stomping ground. The 1988 Democratic Convention that nominated Michael Dukakis as the party’s candidate helped open up a whole new market for the company, while Opera North took a delivery of one of the QM500-TD versions of the console and started applying rock touring techniques to their lighting, not only enhancing their performance but also dramatically shortening their set up times, and giving the Avolites strap line “from Rock to Opera”. Other theatre clients soon followed, and then there was Eurovision 1989…
Douze points for Avolites
Eurovision 1989 was one of those landmark events in the company’s history where its technology was given the appropriately large stage and a big audience — 500 million was claimed at the time — to really show off its capabilities. Held in Lausanne, Switzerland, thanks to Celine Dion’s victory the year before, it was won by Yugoslavia’s Riva with the song ‘Rock Me’.
Basel-based Power Light used primarily UK-based companies to fulfil its lighting, rigging and trussing contract. At the centre of this was control by Avolites with the first of the QM500-TDs to be deployed in anger. In fact, so new was it that a QM500-90 and a Q-Patch were on standby in case of any problems (they were not needed) Hardware designer Richard Salzedo together with the company’s senior software engineer at the time Shahid Anwar spent 10 days in Lausanne offering support making instant modifications as needed to the code, using invaluable feedback from its operator, Power Light’s Felix Riva.
Lighting design was by Claude Egger and Nicholas de Courten, and the result of the system they put in place was an at the time game-changing flexibility that allowed them to stage various scenes in a huge number of permutations. “Egger and de Courten could produce the ‘look’ they wanted by changing colour, movement, and setting to suit the situation, and the flexibility of both the instruments and the design was the key to the show’s visual success,” wrote Lighting & Sound International at the time.
Such flexibility is a given in today’s industry that it is hard to put it into context quite how revolutionary all this was. But the way that the mood of the show could switch from the high-tempo introductory run through of Dion’s previous year’s winner, to softer slow-tempo ballads with hands on instant intervention enabling “plenty of room for more subtle movement and colour variation” the combination of programmed and hands on control was something new and something exciting.
“All in all it was a successful launch for the QM500-TD to a worldwide audience,” commented company MD at the time, Derek Halliday, with a nicely nuanced degree of understatement.
QM500
The original QM500 was genuinely ground-breaking; a two metre long, 180 channel Goliath with two fader banks that could be configured to operate as twin 90-way or one 180-way presets.
It was based on the analogue 80-100 but added a microprocessor, in this case the Motorola 6809, which had enough memory — 64kb — to store 500 states. The resulting show storage for the very earliest models was via standard cassette tape, a system that will be familiar to anyone who came across a Commodore 64 around the same time period, while later models shifted things up a gear with the 3.5in floppy.
One other innovation it introduced was programmability. Indeed, it had to be programmed rather than just busked, which had profound implications for the way that show rehearsals were managed both then and into the future.
A massive 660-channel version was built specially for the Hippodrome nightclub in London, while there was also a theatre desk version designed and built, the QM500-TD, where faders were replaced by a central screen, which proved to be just as influential in its field as the original unit was in the rock lighting space.
Increasing intelligence
The 90s was a challenging decade for the industry, but also a hugely exciting one as a new breed of intelligent lighting products made their way into the Lighting Designer’s toy box. The result was a steady trend of bigger and more spectacular shows that started to hint at the multimedia extravaganzas that were to come.
For Avolites itself it was a time of change too. The company — along with a whole host of other media tech companies, including, Quantel, SLL, and Technicolor — had been bought by a rapidly expanding media company in the late 80s, but the relationship didn’t last and it quickly returned back to private ownership in 1991 following a MBO led by three employees: Richard Salzedo (who is currently Chairman), Steve Warren (currently New Business Director), and Meena Varatharajan (retired Finance Director).
It hasn’t looked back since.
The new intelligent lighting products needed equally intelligent consoles to control them, and during that decade the company introduced new products aimed to do just that, releasing the Rolacue Sapphire, Pearl 2000 (released 1995), Sapphire 2000 (released 1998) and Diamond II/III consoles. These consoles were based on the Motorola 68340 processors combined with a TI Digital Signal Processor which was a new innovation at the time. In 1996 the company updated the FD dimmer, replacing it with the all digital Art 4000.
During the 2000s the dimmer product range was upgraded, resulting in the Art 2000 series of racks; the Art 2000i installation racks and – in the later part of the decade – the PowerCube dimmer/distribution units. In 2001, Avolites launched the Diamond 4 range of control consoles, which was based on an industrial PC motherboard instead of custom-made hardware reliant on Motorola and TI processors.
Enter Titan
This was an important inflection point for the company. Although the custom hardware consoles were sold and updated in stages during the 2000s, in common with a lot of other tech companies at the time Avolites decided to pivot towards using off-the-shelf robust industrial design motherboards and communication protocols and standards. Letting go of the proprietary, bespoke electronics was not an easy decision, but the pace of technological change was accelerating to such an extent that there was no way that even medium to large sized enterprises could keep up. For an influential yet still relatively small specialist such as Avolites the choice was simple: hitch up to the technology bandwagon or slide into niche insignificance.
Avolites decided on the former approach and moved software development towards the Windows platform running on industrial grade PC motherboards. This raised some interesting challenges. The Pearl Expert was the first console to utilise the new electronic hardware approach, with the Diamond 4 on the roadmap for soon after. Previously each console had had bespoke software written for each console, writing specific code for propriety designed electronics hardware was time consuming, inflexible, and made iterating the code difficult. So a modular approach was taken with the Pearl Expert featuring an array of USB-connected panels, that ensured it was going to be flexible to adapt and evolve as technology changed, as well as meaning that the software development for the Diamond 4 and subsequent consoles didn’t have to reinvent the wheel.
This deliberate switch went on to lead to the birth of the Titan software platform in 2009, with version one switchable between the “classic” Pearl software but running on a PC or the new Titan software. This software-centric approach over a hardware-driven one meant that future innovations and feature development were much faster, while the modular approach allowed for new features to be easily replicated across the console range.
The next major development was the introduction of the Tiger Touch control surface for the Titan software, which added the flexibility of a touchscreen to the normal armoury of physical buttons and faders, giving its users greater functionality and paved the way for a flexible software design and future developments. Indeed, many of the features that have become well known and used throughout the industry, as well as across many other lighting control software platforms, were first introduced in Titan, to name but a few, the Colour Picker, Key Frame Shapes, Quick Sketch, Pixel Mapper, and Scene Master.
A dozen years later, it is still being aggressively developed. Titan v15, which was released early in 2021, includes the highly-anticipated Timeline feature set that essentially allows timecoded shows to be programmed and edited using visually-led tools. This dramatically increases the speed with which users can set up the full range of Avolites lighting and video effects for a project, giving designers more time for creativity and experimentation.
The next 45 years
As befits a company with such a storied history as Avolites, it has absolutely refused to stand still. A move into media servers saw the launch of the ‘Ai’ range, which was used in the opening and closing ceremonies of the London 2012 Olympics to perform video mapping across the audience seats, setting an as yet unchallenged Guinness World Record for the largest landscape video display consisting of 634,500 individual light sources.
Meanwhile, reflecting the almost ubiquitous use of video alongside lighting, the pioneering, industry leading Synergy software feature set included as part of Titan, was launched in October 2019, allowing video and lighting to be used as one for the first time by everyone, and not just programming professionals. This was a true Avolites innovation, and demonstrated the company’s continued commitment to fully integrating the visual canvas through one control solution.
And 2021 saw the launch of the new flagship console, the Diamond 9, created in consultation with leading visual and expert industrial designers. Born out of all of the company’s 45 years of experience in control and designed with eyes fixed firmly on the future, the D9’s programming surface features vast screen real-estate in the shape of 11 ultra-bright touch screens, including 3 main workspace screens, 3 for media preview, and specific screens for attribute control and softkey short cuts. The new motorised touch sensitive Penny & Giles faders and new encoders each have their own RGB bar graphs so levels can be monitored at a glance. There’s a return of the backlit integrated keyboard. And perhaps the most interesting side of the D9 though, is the right-hand side with 5 encoder wheels, a T bar for controlling scene masters and a new set of bespoke buttons carefully positioned so that finding them is second nature. All are, of course, seamlessly integrated with the Titan software.
The D9 bridges to the past and is the future. It features updated versions of the sort of physical controls that would have been familiar to most of Lighting Designers that first worked with Avolites equipment in the 1970s, while boasting the sort of advanced capabilities that mean it can sit right in the centre of 2021’s increasingly breathtaking shows; where lights, video and special effects are orchestrated in complete sync with the music and stage performances that drive them.
Where the industry goes next and the degree to which virtual environments will start to impinge on the physical is a matter of some debate. But one thing is certain, Avolites will be at the heart of the most creative shows and the very forefront of lighting design, as it has been for 45 years so far: driving the technology forward and empowering Lighting Designers to create ever greater visual spectaculars.
An old advert from a 1980s magazine for an Avolites QM500 bears the slogan ‘making light work’. It’s about a lot more than that now, it’s about making light and the whole visual canvas dance.